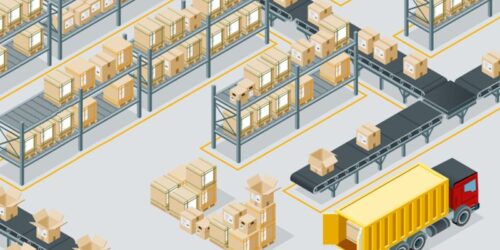
Ever changing industries call for more and more new trends, but this one may be one of the most important for keeping your employees safe and your costs down. Forklifts have been a part of the manufacturing industry since they were invented in 1906, and their use hasn’t changed much since. After over a 100-year run, it may be time for many forklifts to retire.
Forklift Accident Data
OSHA estimates that there are 110,000 forklifts accidents each year. Along with this, approximately every 3 days someone in the US is killed in a forklift related accident. Almost 80% of forklift accidents involve a pedestrian, and 1 in 6 of all workplace fatalities in the U.S. are forklift related.
NIOSH states that the three most common types of injuries occur when: A forklift overturns; workers are struck, crushed, or pinned by a forklift; and workers fall from a forklift.
As reported by The National Safety Council Forklift,
accidents cost employers an average of $48,000
per single work-related disabling injury and $1,390,000 per death. In addition to those costs, according to
OSHA, unsafe working environments can lead to OSHA citations resulting in
penalties that range anywhere from $7,000
to $70,000 per citation.
It is approximated that $135 million immediate costs are incurred due to forklift accidents. In addition to costly payouts, companies also must be concerned with costly litigation, their reputation in the market, and any additional machinery repairs.
Automation To Take Over Material Handling
Our goal with our AGC’s was to develop a system that limits the number of forklifts on the floor to decrease accidents and increase ROI, and we accomplished just that.
AGCs are a type of Automated Guided Vehicle (AGV) that follow magnetic tape paths with RFID readers that direct them where to go. Our carts are designed to deliver high capacity loads, up to 12,000 pounds, and utilize off-the-shelf components with heavy duty steel construction.
AGC’s tunnel under their loads to keep a low-profile on the floor. They also have two laser scanners, with programmable fields, to scan for objects that may be in the way. When a cart detects an obstruction in its path it will stop and send an alert to the central traffic control system. With automatic opportunity or scheduled charging, you can decide when and how long the carts run.
Some added benefits of the AGC system are the reduction of overhead labor costs and increased order processing efficiency. On average, three AGCs complete 500 orders within a 24-hour period.
Automation is taking over the manufacturing industry, causing fewer employee accidents and mistakes, while also increasing ROI. If you are looking to increase success in your company, it is imperative that you see if automated guided carts are right for you. Check out our AGC on our website or contact us today for more details on how our AGC can improve processes in your facility.
Sources:
“Designing for Material Handling Excellence.” The Network Effect, 18 Feb. 2015, supplychainbeyond.com/designing-material-handling-excellence/.
“Forklift Free: Driving Safety and Efficiency.” Seegrid, seegrid.com/blog/forklift-free-driving-safety-and-efficiency/.
Reddy, Emery |. “OSHA Focuses on Forklift Hazards.” Emery Reddy, 8 July 2011, www.emeryreddy.com/2011/07/osha-focuses-on-forklift-hazards/.
White Paper – Towards Improved Forklift Safety . 2009, www.nist.gov/sites/default/files/documents/el/isd/ms/PerMIS-09-Forklift-Safety-WhitePaper.pdf.